In this section of the tutorial, you will build
a standard 3-pole, 2-zero voltage-mode compensator using a built-in parameterized OpAmp and
passive components.
After finishing this section, you will have a
complete closed-loop synchronous buck switching power supply model like the following: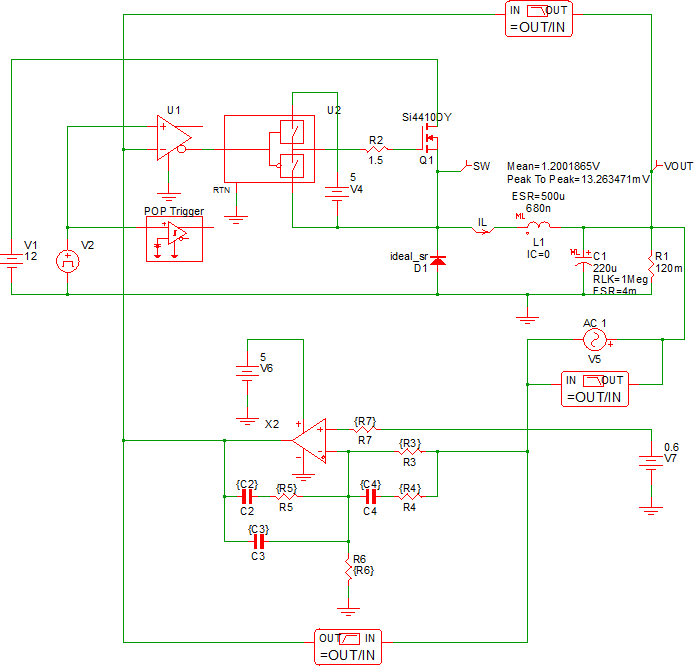
Key Concepts
This topic addresses the following key concepts:
- Symbols can use variables, or parameterized values, that help with schematic reuse. For
maximum flexibility, the compensator schematic uses parameterized values.
- Each schematic has a command (F11) window which stores analysis directives and variable
statements. The text in the F11 window is included in the simulation deck.
- Parameter values can be assigned or calculated in the command (F11) window.
What You Will Learn
- How to parameterize symbols using expressions and the F11 window.
- Why, based on how POP works, choosing the switching node as the periodic input in
section 3.2 Set up a POP Analysis was not the ideal choice.
- How to solve a common POP simulation error by selecting a different POP trigger
schematic node.
- How to add parameter debug statements to the F11 window.
5.1.1 Build the Compensator Schematic
In the previous chapters you
learned how to place symbols using the parts selector and keyboard shortcuts. Starting with
the
9_SIMPLIS_tutorial_buck_converter.sxsch schematic, use the
following table of shortcuts and the illustration below as a guide to place the compensator
symbols in the area below the power stage.
Keyboard Shortcuts for Placing Compensator Symbols
Symbol |
Parts Selector Location |
Keyboard Shortcut |
Multi-Level Parameterized Opamp
(Version 8.0+) |
Analog Functions |
none |
Resistor |
Commonly Used Parts |
4 |
Capacitor (Ideal) |
Commonly Used Parts |
C |
Power Supply |
Commonly Used Parts |
V |
Bode Plot Probe (Gain/Phase) w/
Measurements |
Commonly Used Parts |
none |
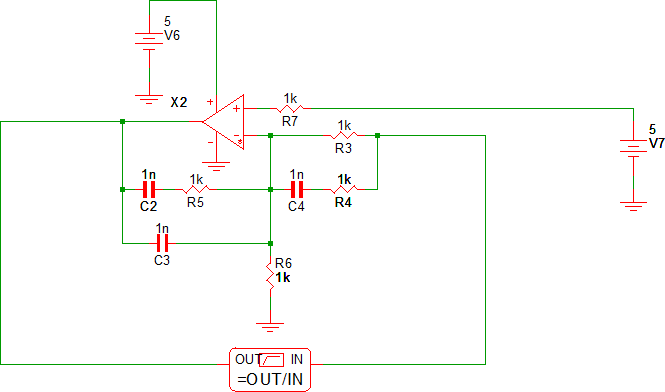
▲ back to top
5.1.2 Assign Parameterized Values to Symbols
After you have the drawn your schematic, double
check that each resistor and capacitor has the reference designator as shown in the
schematic above.
Important: The design procedure uses these reference
designators to calculate values; therefore, they must match the illustration, or the
calculated values will be assigned to the wrong components.
If your reference
designators differ from those in the above image, follow these steps to change them:
- Select the resistor or capacitor symbol.
- Press Shift+F8.
Result: A dialog opens for you to
enter a new reference designator.
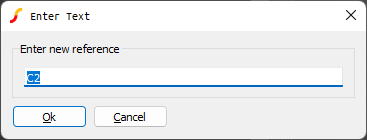
- Enter the reference designator as shown in the schematic above.
When you assign parameterized
values, you enclose the parameter name or expression in curly braces. In this tutorial you
will use the reference designator text as the parameter name, for example, the parameterized
value for the resistor R3 will be {R3}.
CAUTION:
Both the
opening { and closing curly brace } characters are required. Without an
opening and closing curly brace, the expression will not evaluate correctly and the circuit
will not simulate.
To assign parameterized values to the resistor and capacitor
symbols, follow these steps:
- Double click on each resistor or capacitor and change the value of the resistance or
capacitance to a parameterized value.
- For the DC source V7, change the value to 0.6V.
Tip: This
will be the reference voltage for the compensator.
Your compensator schematic should now look like the following:
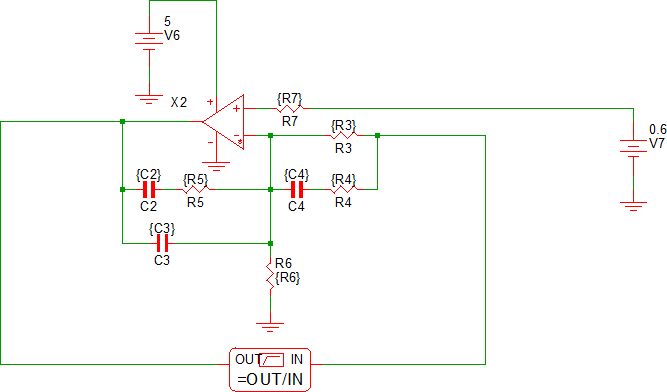
▲ back to top
5.1.3 Connect the Compensator to
the Power Stage
You will now close the feedback loop by
connecting the compensator to the power stage.
To connect the compensator to the power stage,
follow these steps:
- Delete V3, the DC source which was the duty cycle control.
- Delete the wires connecting the AC source V5 to the comparator U1
input.
- Move V5 to the right side of the schematic.
Tip: This will become
the loop perturbation source.
- Wire the compensator to the power stage as shown in the image below:
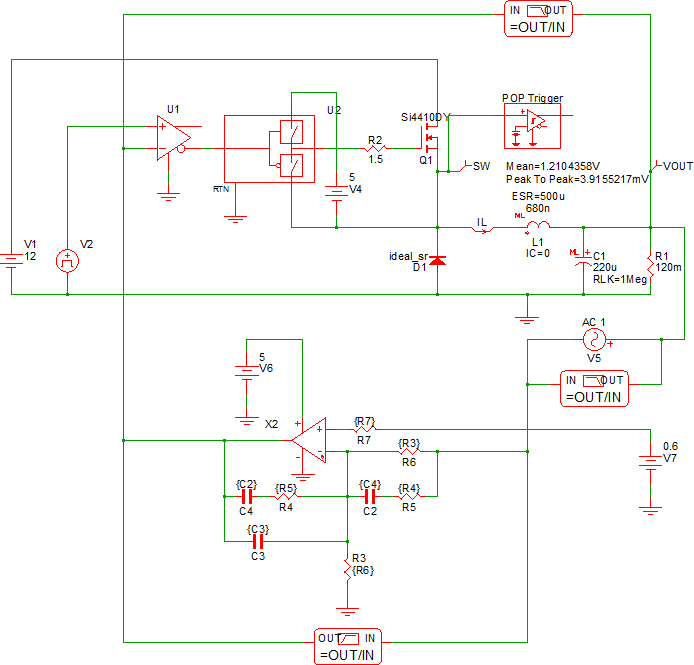
- Add the Bode Plot Probe across the V5 source.
Tip: This will probe
the loop gain of the converter.
- The output capacitor in this design has no ESR. In the previous simulations this was
not an issue, but when the compensator is added, the ESR plays a role in calculating the
compensator values. To include an ESR on this multi-level capacitor, double-click on
C1 and set the model level to 2, and assign an ESR of 4mΩ.
Result: The ESR value of 4m is displayed on the schematic.
This indicates the model for the capacitor now includes an ESR.
5.3.4 Disable Power Stage and Compensator Bode Plot Probes
You now have three Bode Plot probes on the
schematic and each probe will output a gain and phase curve with the default names of
Gain and Phase. This will make a confusing graph with six curves, so in the
next procedure, you will turn off the compensator and power stage probes as well as rename
the curves generated by these probes. This will allow easy debugging later when you might
want to see the power stage or compensator bode plots.
To turn off the probes and rename the output
curves, follow these steps:
- Double click on the compensator bode plot probe and rename the gain and phase curves
to Compensator Gain and Compensator Phase.
- Check Disable gain/phase at the top of the dialog, and then click
Ok.
- Double click on the power stage bode plot probe and rename the gain and phase curves
to Plant Gain and Plant Phase.
- Check Disable gain/phase at the top of the dialog, and then click
Ok.
▲ back to top
5.1.5 Enter Parameter Values in the Command (F11) Window
In 5.1.3 Connect the Compensator to the Power Stage, you added
parameterized values to each symbol by enclosing the variable name in curly braces {
}. The curly braces form an expression and tell the program to stop and evaluate the
expression; in this case, the program simply substitutes the value for the variables
R3, C2, etc. in place of the expressions, {R3}, {C2}, etc. At
this point in the design, the values for the compensator are not defined. Next, you will
assign values to these variables using .VAR statements.
Explaining how to compensate a 3-Pole/2-Zero voltage mode compensator is beyond the scope
of this tutorial. Instead of dwelling on the compensator design process, which was taken
from this application note, you will copy the text lines from this tutorial
and paste them into the F11 window of the schematic. The .VAR lines are actually an entire
design process taken from a spreadsheet and turned into variable statements.
To enter the parameter values in the F11 window, follow these steps.
- Copy all text in the box below:
******************************
*** Circuit Specifications ***
******************************
.VAR VIN = 12
.VAR VRAMP = 1
.VAR L = 680n
.VAR C = 220u
.VAR VOUT = 1.2
.VAR VREF = 0.6
.VAR ESR = 4m
.VAR FXOVER = 80k
.VAR FSW = 500k
*** Calculated Parameters - not used in calculations
.VAR FLC = 13012.31
.VAR FESR = 180857.89
.SUBCKT ONE_PULSE_SOURCE_I 1 2 vars: _T_RISE=0 _T_FALL=0 _DELAY=0 _V1=0 _V2=1 _PWIDTH=1u
.NODE_MAP P 1
.NODE_MAP N 2
{'*'} _DELAY : {_DELAY}
{'*'} _T_RISE : {_T_RISE}
{'*'} _PWIDTH : {_PWIDTH}
I1 1 2 PWL NSEG=4 X0=0 Y0={_V1} X1={_DELAY} Y1={_V1} X2={_DELAY+_T_RISE} Y2={_V2} X3={_DELAY+_T_RISE+_PWIDTH} Y3={_V2} X4={_DELAY+_T_RISE+_PWIDTH+_T_FALL} Y4={_V1}
.ENDS
*********************************************************
*** Compensator Design - Find desired poles and zeros ***
*********************************************************
*** Place Second Zero at LC
.VAR FZ2 = {1/(2*pi*SQRT(L*C))}
*** Place First Zero at 75% of FZ2
.VAR FZ1 = {0.75*FZ2}
*** Place Second Pole (1st pole at origin) at ESR zero
.VAR FP2 = {1/(2*pi*ESR*C)}
*** You will get better performance putting the pole
*** above ESR zero (different than design procedure)
.VAR FP2 = {0.75*FSW}
*** Place Third Pole at 1/2 the switching frequency
.VAR FP3 = {0.5*FSW}
*******************************************************************
*** Compensator Design - Assign resistor and capacitor values ***
*** The design procedure was taken from IR/Infineon an-1162.pdf ***
*** ***
*** http://www.irf.com/technical-info/appnotes/an-1162.pdf ***
*******************************************************************
*** Choose C4 to be 2.2nF This is somewhat arbitrary,
*** it sets the magnitude of other compensator values.
.VAR C4 = 2.2n
*** From C4 and FP2, Calculate R4
.VAR R4 = {1/(2*pi*C4*FP2)}
*** From C4, R4 and FZ2, Calculate R3
.VAR R3 = {1/(2*pi*C4*FZ2)-R4}
*** From R3, VREF and Nominal VOUT, Calculate R6
.VAR R6 = {R3*VREF/(VOUT-VREF)}
*** Calculate R7 as the parallel combination of R3 and R6
.VAR R7 = {R3*R6/(R3+R6)}
*** Calculate R5. Modify VRAMP to adjust final loop characteristics
.VAR R5 = {2*pi*FXOVER*L*C*VRAMP/(VIN*C4)}
*** From R5 and FZ1, Calculate C2
.VAR C2 = {1/(2*pi*R5*FZ1)}
*** From R5 and FP3, Calculate C3
.VAR C3 = {1/(2*pi*R5*FP3)}
*****************************************************************
*** Debug. These statements come out in the deck as comments. ***
*** Simulator -> Edit Netlist (after preprocess) opens file ***
*****************************************************************
{'*'} FZ2 : {FZ2}
{'*'} FZ1 : {FZ1}
{'*'} FP2 : {FP2}
{'*'} FP3 : {FP3}
{'*'} C4 : {C4}
{'*'} R4 : {R4}
{'*'} R3 : {R3}
{'*'} R6 : {R6}
{'*'} R5 : {R5}
{'*'} C2 : {C2}
{'*'} C3 : {C3}
- In the schematic editor, press F11.
Result: The
command (F11) window opens at the bottom of the schematic.
- Drag the splitter bar between the command (F11) window and the schematic so the command
window and the schematic take approximately 50% of the vertical space.
- In the command window, scroll down past the last statement, which is the
.SIMULATOR DEFAULT
line and use the keyboard shortcut Ctrl+V
to paste the copied text in the F11 window below the .SIMULATOR DEFAULT
line.
Four sections of text are used to parameterize the compensator.
- The first section has design values. The statement .VAR VIN = 12
assigns the number 12 to the variable VIN. Although VIN is not used in the
schematic, it is used in calculations for other variables. You could add VIN to the
input source as a parameter {VIN}.
- The second section has the calculations for the compensator poles and zeros. The
statement .VAR FZ2 = {1/(2*pi*SQRT(L*C))} assigns a value to the
FZ2 variable. In this case, the value is the resonant frequency of the converter.
Note: The variables L and C, as well as the global constant pi and
the built-in function SRQT(), are used in the expression on the right side of the
equals sign. The variables L and C must be assigned before they are used;
therefore, the order of the lines in the window is important. The global constant
pi and the function SQRT() are defined by the program.
- The third section calculates the actual resistor and capacitor values from the first
section of the circuit specifications and the poles and zeros from the second
section.
- The final section has debug statements. These statements output comments to the
simulation deck so you can easily debug which values are being used in the compensator.
For example, the values in the design will output the following to the deck file:
* FZ2 : 13012.3080131893
* FZ1 : 9759.23100989196
* FP2 : 375000
* FP3 : 250000
* C4 : 2.2e-009
* R4 : 192.915082535631
* R3 : 5366.67940889006
* R6 : 5366.67940889006
* R5 : 2848.37733925475
* C2 : 5.72541552580328e-009
* C3 : 2.23502610975745e-010
A schematic saved at this state can be
downloaded here:
10_SIMPLIS_tutorial_buck_converter.sxsch.
▲ back to top
5.1.6 Try to Simulate the Design
When you try to simulate this design you will
get simulation errors and SIMPLIS will automatically run a transient simulation so you can
see what might be causing the errors. The waveforms will appear as follows:
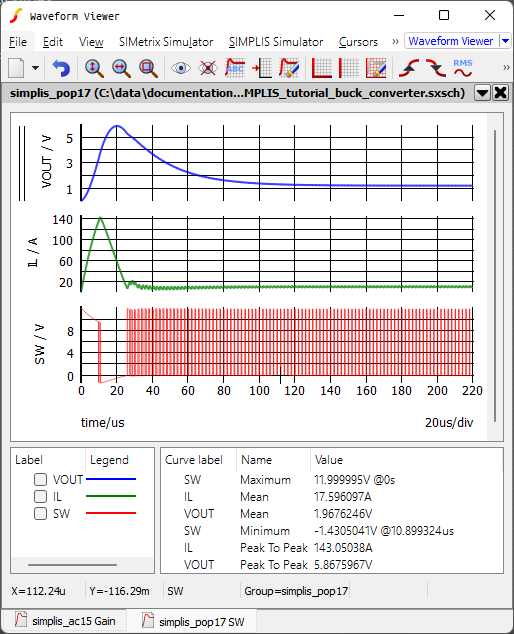
Clearly, the converter reaches a steady
state operating point at the end of the transient simulation so you know that the loop is
stable. The cause for the simulation errors is as follows:
- The initial conditions for the converter cause the error: the output voltage starts at
0V, and the compensator attempts to correct this with several cycles of full duty cycle.
- The modulator, at this stage of development, does not have either a duty cycle limit or
a current limit; as a result, the inductor current reaches a high value before the output
voltage overshoots.
- After the output voltage overshoots the reference, the compensator turns off the switch
for several switching periods.
- During the portion of the simulation where there is no switching, SIMPLIS is monitoring
the POP Trigger and at 4.4μs, when twice the maximum POP period is reached, SIMPLIS thinks
something has gone wrong with the circuit and outputs the following warning and
error:
*** WARNINGS REPORTED BY SIMPLIS ***
****************************************
<<<<<<<< Error Message ID: 5020 >>>>>>>>
Periodic Operating-Pt Analysis:
Reaching a time duration equal to
`4.40000e-006' without registering the
triggering condition that defines
the start of a period. Check your
circuit and/or initial conditions.
*** END SIMPLIS WARNING REPORT ***
*** ERRORS REPORTED BY SIMPLIS ***
****************************************
<<<<<<<< Error Message ID: 5039 >>>>>>>>
The periodic operating point (POP) analysis
has failed to converge. AC analysis will
not be performed.
*** END SIMPLIS ERROR REPORT ***
Two
possible solutions exist:
- Solution 1: Change the initial conditions of the circuit to initialize the
circuit closer to the steady-state conditions. The compensator will then make small
corrections to bring the converter into steady-state; the duty cycle will never reach 0
or 100%; and the POP analysis will succeed. This is a good design practice and you will
probably need to do this at some point, especially with a more complex circuit.
- Solution 2: Change the location of the POP trigger gate so that the input
signal crosses the POP trigger threshold on every switching cycle, independent of the
commanded duty cycle. Since the oscillator node is independent of the commanded duty
cycle, this is a good choice for the POP trigger node.
For this tutorial, you will use Solution 2, moving the POP trigger gate to the
oscillator node and changing the threshold of the POP trigger gate to
0.5V.
▲ back to top
5.1.7 Move the POP Trigger Gate
To move the POP trigger gate to the oscillator node, follow these steps:
- Click on the POP trigger symbol to select it.
- Press Ctrl+X to cut the symbol.
- Press Ctrl+V to paste the symbol.
- Place the POP trigger symbol to the right of the oscillator V2.
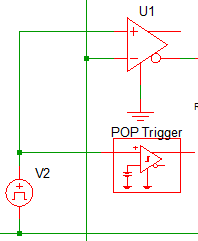
- Double click on the POP trigger symbol, and change the Threshold parameter to
0.5V and click Ok to save your changes.
- Wire the input of the POP Trigger to V2 as shown in the image.
▲ back to top
5.1.8 Verify Loop Stability
The circuit should now run the POP and AC
analysis configured earlier in the tutorial; however, the maximum frequency for the AC sweep
is greater than the switching frequency which will result in plots with a small scale due to
the high frequency noise.
To change the maximum frequency, follow these
steps:
- From the schematic editor menu, select .
- In the Sweep parameters section on the AC tab, change the Stop frequency to
400kHz.
- Click Ok, or press F9 to run the simulation.
Result: The simulation runs without errors and the bode plot for the
converter is output to the waveform viewer. The Gain Crossover Frequency is 98kHz, the
Phase Margin is 48 degrees and the Gain Margin is 13.5dB.
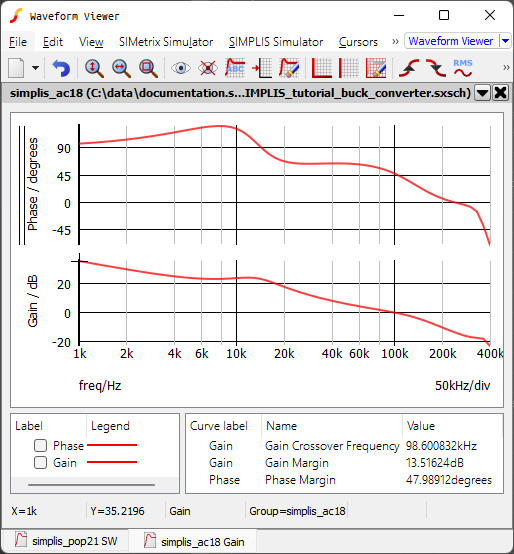
▲ back to top
5.1.9 Save your Schematic
To save your schematic, follow these steps:
- Click anywhere in the schematic to bring the schematic viewer in to focus.
- From the menu bar, select .
- Navigate to your working directory where you are saving your schematics.
- Name the file 11_my_buck_converter.sxsch.
A schematic saved at this state can be downloaded here:
11_SIMPLIS_tutorial_buck_converter.sxsch.
▲ back to top